Product & Service
Product Liability and Safety Systems
Policy
SK Gas supports LPG quality and safety management for our customers, ensuring they can use LPG safely. We aim to enhance LPG quality and safety management to prevent accidents and foster a positive perception of LPG among consumers.
1. LPG Quality and Safety Management Governance
We strengthen LPG quality and safety management, with major issues reviewed by the ESG Committee within the Board of Directors, alongside health and safety issues.
2. Strengthening LPG Quality Management
We operate QC and QM organizations to perform quality inspections based on inspection procedures and quality standards from LPG import to storage and sale. In accordance with legal quality standards set by the Ministry of Industry, we regularly inspect and manage products at Ulsan, Pyeongtaek, and refueling stations for seven criteria (composition, sulfur content, vapor pressure, density, residue, copper corrosion, and moisture) to ensure compliance with LPG quality standards.
Metrics
SK Gas has achieved a 100% compliance rate with legal quality inspection standards from 2021 to 2023. To maintain this record, the company has established a product quality management roadmap and is implementing a systematic management approach. The company transparently discloses its achievements and goals in product and service safety management through the ESG Data Hub.
LPG Quality Standards
LPG product quality standard (MSDS) information can be downloaded from the Business Overview-LPG-LPG Overview/Quality Standards section on our website.
Client Safety Management
Safe LPG Ecosystem
We operate a safety ecosystem program to ensure the safe and stable supply of LPG. We support legal inspections and safety checks for customer facilities to ensure the integrity of their equipment, and conduct activities to enhance the SHE capabilities of customer managers and identify facility risk factors.
From 2022 to 2023, we collaborated with the Korea Gas Safety Corporation to conduct safety inspections of customer facilities, identify operational difficulties through interviews with customer managers, analyze risk factors, and establish a four-stage roadmap from building a safety management system to establishing a safety culture. To enhance accident prevention and safety management at customer sites, we have established and are operating a safety technology group under the company-wide health and safety management organization.
Roadmap
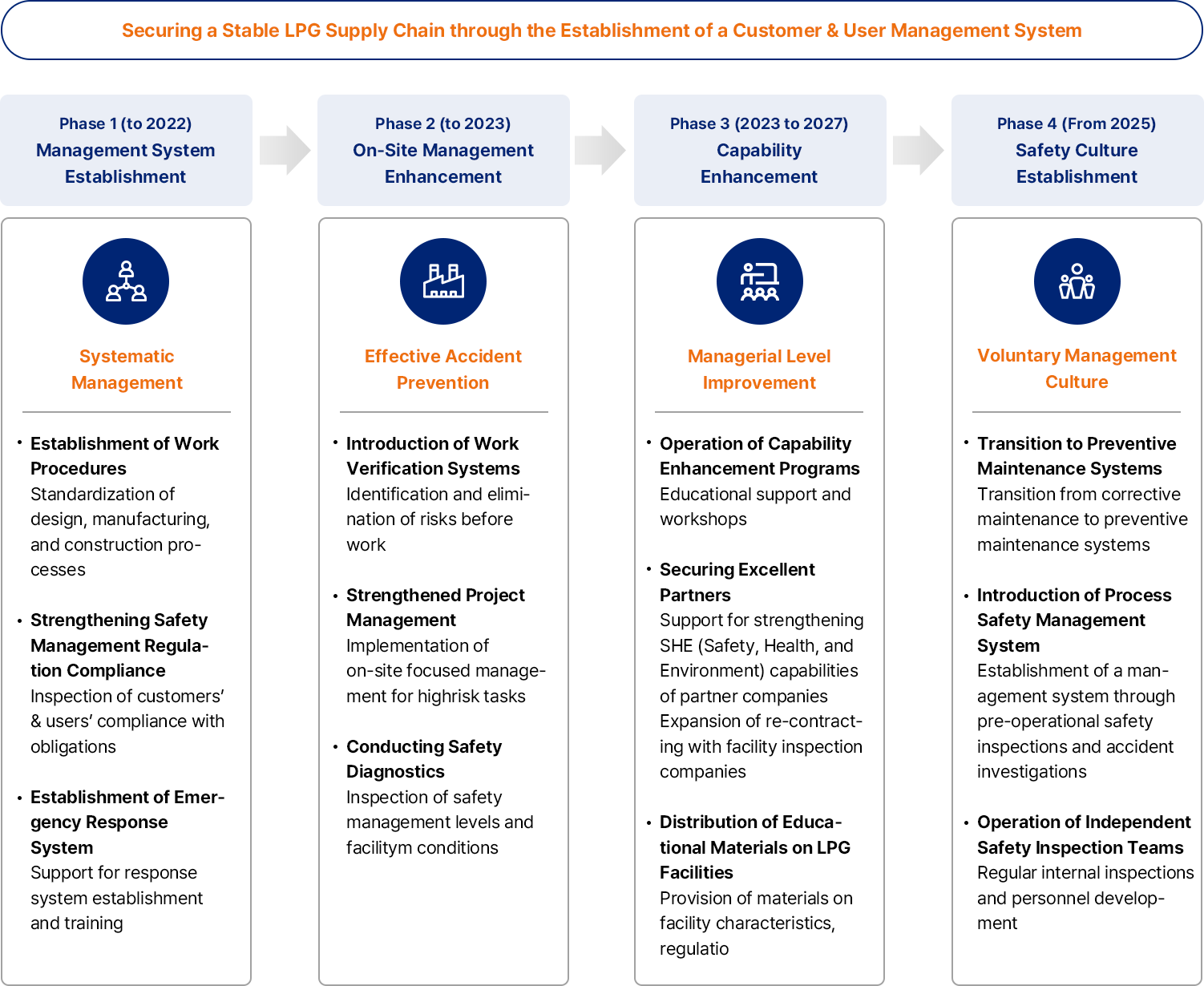

Ensuring a stable LPG supply chain through customer management system establishment
-
Phase 1 (~2022): Systematic Management
- Establishing work procedures: design/manufacturing/construction procedures
- Strengthening compliance with safety management regulations: checking the fulfillment of customer obligations
- Establishing an emergency response system: building and supporting response systems and drills
-
Phase 2 (~2023): Practical Accident Prevention
- Introducing a work confirmation system: identifying and eliminating risks before work
- Strengthening management of high-risk construction: selecting high-risk tasks and implementing on-site focused construction management
- Conducting detailed safety diagnostics: checking safety management levels and facility status
-
Phase 3 (2023-2024): Improving Manager Levels
- Operating capacity-building programs: providing training support and workshops
- Securing excellent partners: supporting the enhancement of partner SHE capabilities, expanding re-contracts with facility inspection companies
- Distributing educational materials on LPG facilities: providing facility characteristics, regulations, and checklists
-
Phase 4 (2025~): Voluntary Management Culture
- Strengthening preventive maintenance systems: transitioning facility management from post-maintenance to preventive maintenance
- Introducing process safety management systems: establishing a management system through pre-operation safety checks, accident investigations, etc.
- Operating an independent safety inspection team: conducting regular internal inspections and personnel training
Customer Safety Management | 2022 | 2023 | 2024 | 2025 |
---|---|---|---|---|
Achieving Zero Major Accidents | ||||
Improving LPG Facilities |
Developing plans for improving aging LPG facilities |
|||
Preventive maintenance (compressors) |
Preventive maintenance (loading arms/vaporizers) |
Regular preventive maintenance |
||
Upgrading S/B System |
Applying Wego Safety to customers |
Upgrading LPG Facility Systems |
||
Strengthening On-site Work Management |
Developing plans to strengthen on-site safety management |
|||
On-site safety management for high-risk tasks (reinspection of specific equipment) |
Expanding on-site safety management (5 major risk tasks) |
|||
Implementing safety work confirmation system |
Implementing work risk assessments |
|||
Supporting Contractor Safety Management |
Conducting safety awareness surveys and regular safety training for contractors |
|||
Establishing SHE evaluation standards for contractors |
Improving contractor SHE levels through evaluations and consulting |
Tank Lorry Safety
We are strengthening safety management to prevent accidents involving tank lorries transporting our LPG. Based on risk assessment results and driver feedback, we have established an accident prevention program that includes vehicle inspections, education, and infrastructure improvements. We conduct safety inspections of tank lorries entering our bases through partner companies, invite experts from the Korea Gas Safety Corporation to provide safety education for drivers and listen to their suggestions. We also continuously improve infrastructure within our bases to prevent vehicle accidents, such as removing obstacles, painting guidelines, installing speed bumps, and installing heating wires to prevent ground freezing.
Key Programs
SK Gas regularly conducts safety inspection services and on-site compliance checks to proactively identify risk factors, enhance facility improvements, and strengthen preventive maintenance. We report the safety management strategies and execution results to the SHE Committee chaired by the CEO.
Reflecting social expectations for industrial safety and customer requests, we have strengthened improvements for aging LPG facilities at customer sites since 2022. We also distribute emergency response scenarios and support emergency response training during safety inspections to enhance customer safety management.
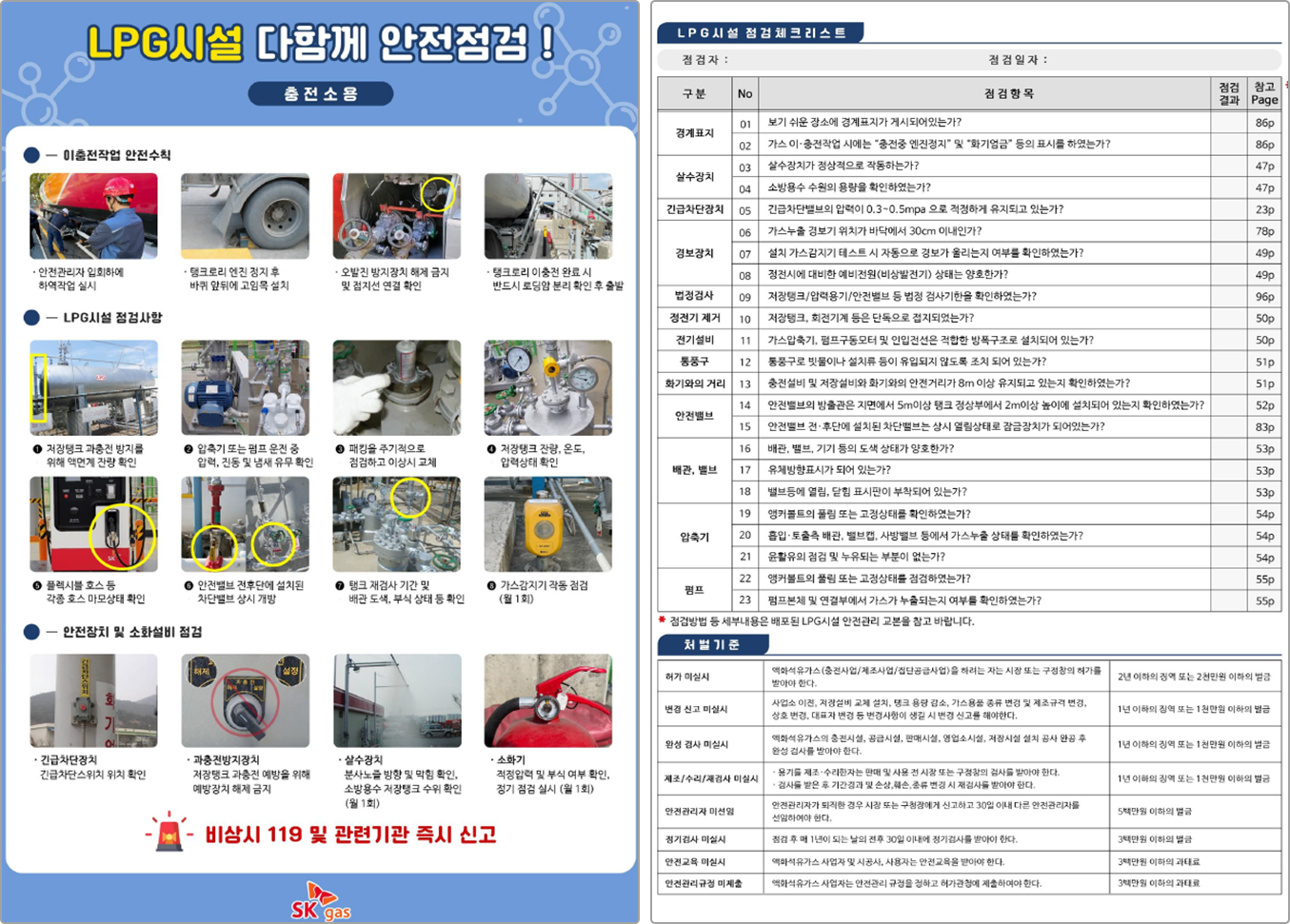
LPG Facility Inspection Manual & Checklist
Additionally, to promote voluntary safety management by the customers, we have provided inspection manuals and checklists, and through on-site coaching, we guide safety activities such as facility inspections and risk assessments, including training on major accident prevention laws for safety managers.
In 2021, SK Gas launched "Wego Safety," a digital safety management service using IoT sensors, the first in the industry. Wego Safety helps refueling stations and bulk businesses timely fulfill safety management duties for small storage tanks and better prepare for safety accidents. We are also digitizing regular inspections in collaboration with the Korea Gas Safety Corporation, expanding daily mobile inspections, and providing expert inspection services for bulk lorry accident prevention, enabling safety managers to focus more on safety checks on-site.
Furthermore, by linking public data from the Ministry of Public Administration and Security with customer location information (GPS), we operate disaster response services to prepare for safety accidents caused by disasters such as wildfires, heavy rains, and landslides.
Consumer Grievance Channel
SK Gas consults on and handles customer grievances in accordance with its Customer Grievance Handling Procedure, Customer Safety Service Procedure, Code of Ethics, and Anti-Bribery Management System Regulations, and transparently discloses its performance in this regard annually.