Health and Safety
H&S Management System
Policy & System
Health and Safety Policy
SK Gas has declared its SHE (Safety, Health, Environment) management policy, placing safety, health, and environment as core values of its management to realize the happiness of all stakeholders. Additionally, SK Gas has established and operates SGRs (Safety Golden Rules), which are essential safety rules that employees and contractors must comply with, and applies a zero-tolerance principle for violations, taking follow-up measures in accordance with internal regulations.
Safety Golden Rules
- 1All work must be carried out following the work permit procedure after obtaining approval.
- 2Ensure fall protection measures are in place for work at heights.
- 3Measure harmful gases and oxygen levels at designated intervals during confined space work.
- 4Establish safety zones and restrict pedestrian access during heavy equipment operations.
- 5Implement fire prevention measures before conducting hot work.
- 6Lockout and tag equipment during maintenance of processes and electrical facilities.
- 7Check for buried objects before excavation work.
- 8No smoking on the premises except in designated areas.
- 9Report safety incidents immediately without concealment.
Health and Safety Management System
Since introducing its company-wide SHE Policy and SHE Management System in 2016, SK Gas has strived to establish a virtuous cycle of SHE (Plan-Do-Check-Action) across all its business sites. The company is dedicated to protecting the health and safety of its members, partner company employees, local communities, and consumers. With the goal of achieving a world-class SHE management system, SK Gas has continuously raised its health and safety management standards in accordance with the roadmap of its SHE Masterplan, which was established in 2021. Furthermore, in 2023, SK Gas confirmed that its health and safety management system aligns with international standards by obtaining ISO 45001 (Occupational Health and Safety Management System) certification, a global standard for health and safety management.The company-wide health and safety management system is operated based on three key regulations, including the Process Safety Management Regulation, along with various procedures such as the Safety Rules Management Procedure, Work Permit Procedure, Industrial Health Management Procedure, Partner Company SHE Management Procedure, and Customer Emergency and Accident Management Procedure. Each year, the health and safety management system undergoes self-assessments and third-party external audits to identify areas for improvement and uncover hazards and risks in the field. These findings are then incorporated into and executed as improvement tasks.
Health and Safety Management System ISO 45001
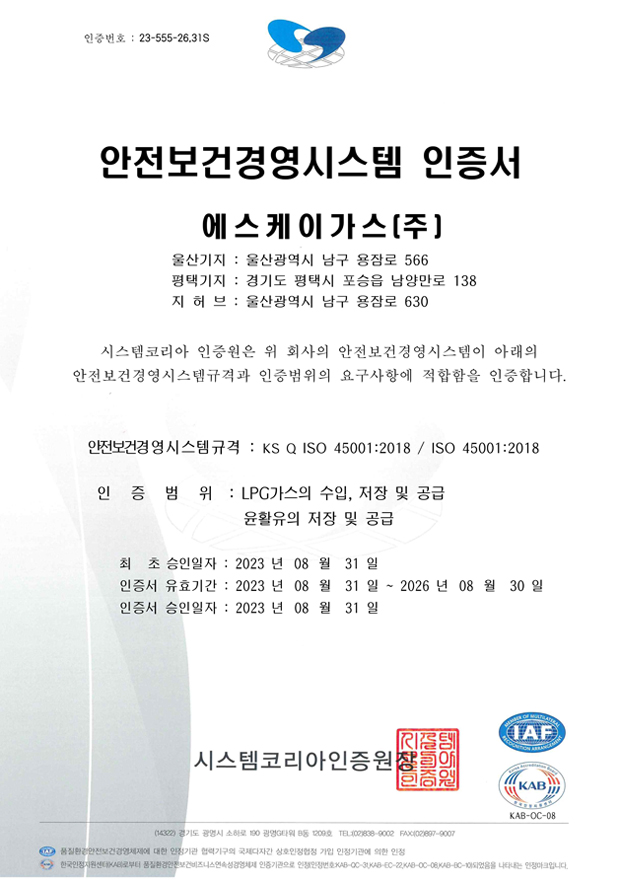
Board and Executive Leadership
In accordance with the ESG Committee Regulations, significant Health and Safety matters are deliberated and reviewed by the ESG Committee within the Board of Directors. When necessary, these matters are submitted to the Board for approval. The CEO provides an annual report to the ESG Committee on various aspects, including Health and Safety performance, plans for the upcoming year, management policies, organizational structure and roles, budget, and facility status. Agenda items reviewed by the ESG Committee are subsequently approved at the full Board of Directors meeting.
For the CEO and responsible executives overseeing industrial Health and Safety, Health and Safety performance indicators, such as the Lost Time Injury Rate (LTIR) and Health and Safety level assessment results, are integrated into their KPIs for evaluation, which directly influences their compensation. The compensation details related to the Health and Safety performance of key executives are disclosed in the
Metrics
To achieve a Global Top-Tier level of health and safety management system, SK Gas has established the SHE Master Plan 2.0, presenting short- and mid-term goals at the Global Top-Tier level for each key performance indicator. The company is actively implementing improvement initiatives based on this roadmap.
In terms of key performance indicators, the industrial safety sector focuses on the number of serious accidents at business sites and customer locations, as well as the Lost Time Injury Rate (LTIR). For the health sector, indicators include the incidence rate of occupational diseases, health management diagnostic programs, and the reduction of high-risk groups such as those with underlying health conditions. Additionally, the integrated field of industrial safety, health, and environment involves the evaluation and management of SHE management diagnosis ratings.
SHE Level Evaluation
Score | Grade | Level | Definition |
---|---|---|---|
95 or above | S | Global Top Tier | Exceeds legal SHE management standards |
90 or above | A+ | Excellent | Meets legal standards and performs SHE activities beyond legal requirements |
80 or above | A | Satisfactory | Meets legal standards and mostly complies with procedures |
70 or above | B+ | Average | Partially meets legal standards and requires improvement in procedural compliance |
60 or above | B | Inadequate | Partially meets legal standards but lacks procedural compliance |
Below 60 | C | Serious | Does not meet legal SHE management standards |
SHE Masterplan 2.0
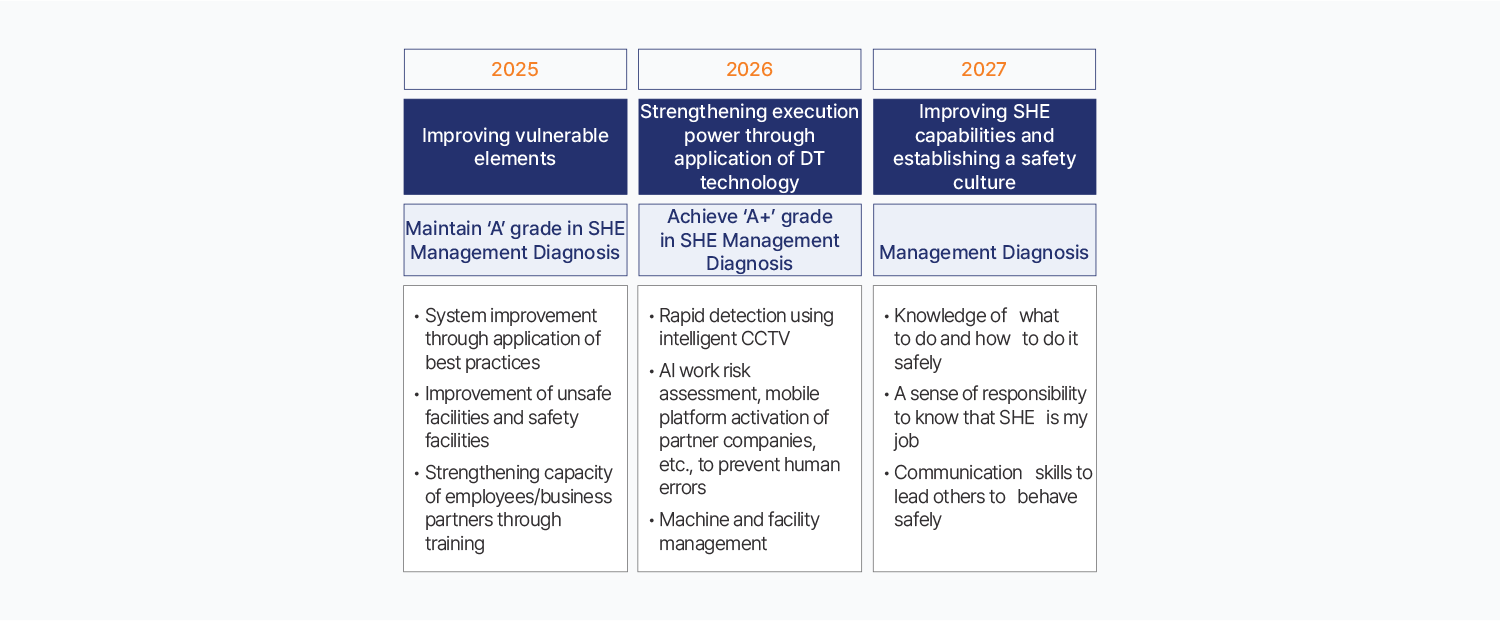
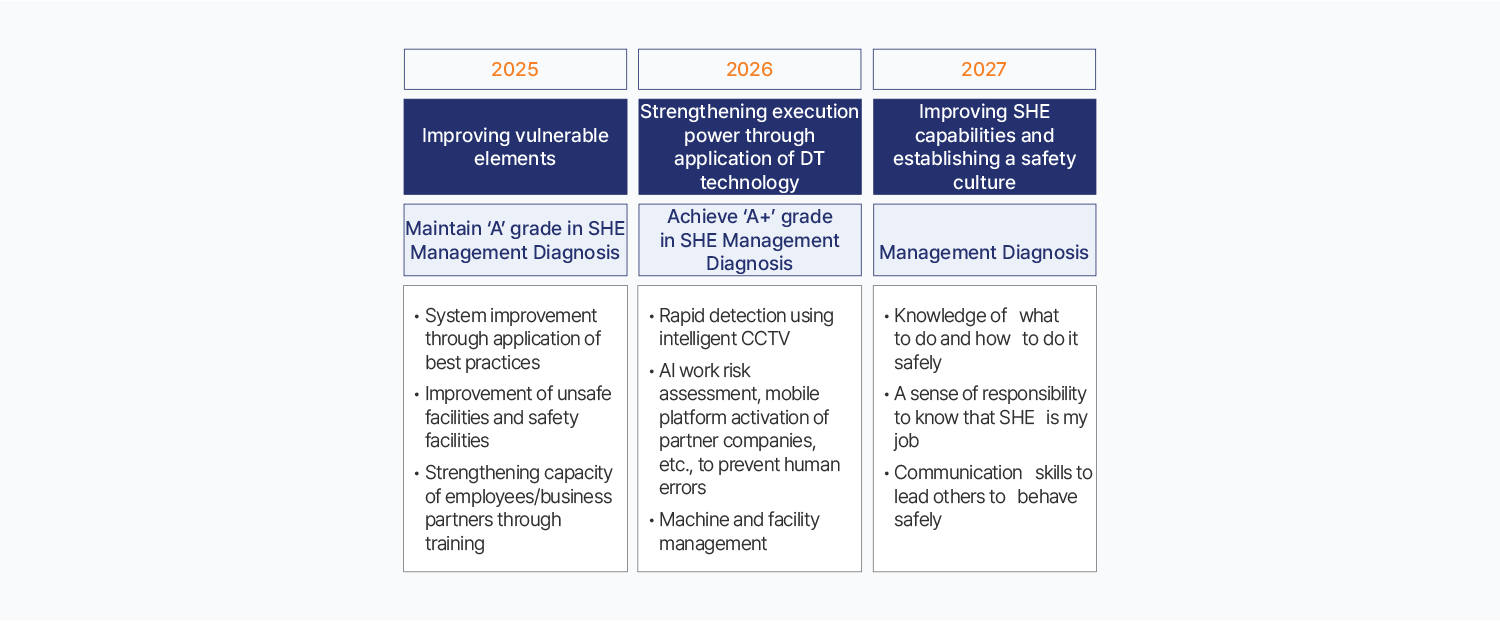
SHE Master Plan 1.0
- 2021: Establishing SHE Foundation
- Develop SHE Master Plan
- Build dedicated SHE team and secure specialized personnel
- Identify and improve harmful and hazardous factors
- 2022: Enhancing SHE System
- Conduct internal SHE audits
- Improve partner management process (evaluate SHE capabilities)
- Introduce safety observation process
- Monitor regulatory changes
- 2023: Strengthening On-site Implementation
- Identify and improve management blind spots
- Enhance education and training
- Establish customer management system
SHE Master Plan 2.0
A+ (90, Excellent)*
- 2024 ~ 2026: Building Bottom-up Safety Culture
- Foster advanced safety culture
- Introduce behavior observation process
- Build Smart Terminal SHE system
- Identify and improve customer vulnerability points
Health Management Milestons
SK Gas operates health check-up implementation status as a key health performance indicator, expanding comprehensive health check-up support to include resident partner companies to consider the health of partner employees as well. Health goals include reducing the incidence rate of occupational diseases, operating health management diagnostic programs, and decreasing high-risk groups, such as individuals with underlying health conditions.
To achieve these goals, SK Gas has established milestones for three major mid- to long-term tasks: identifying health risks, post-risk management, and transitioning to a Smart Management system, thereby enhancing employee health management.
Safety and Health Plan Implementation Schedule
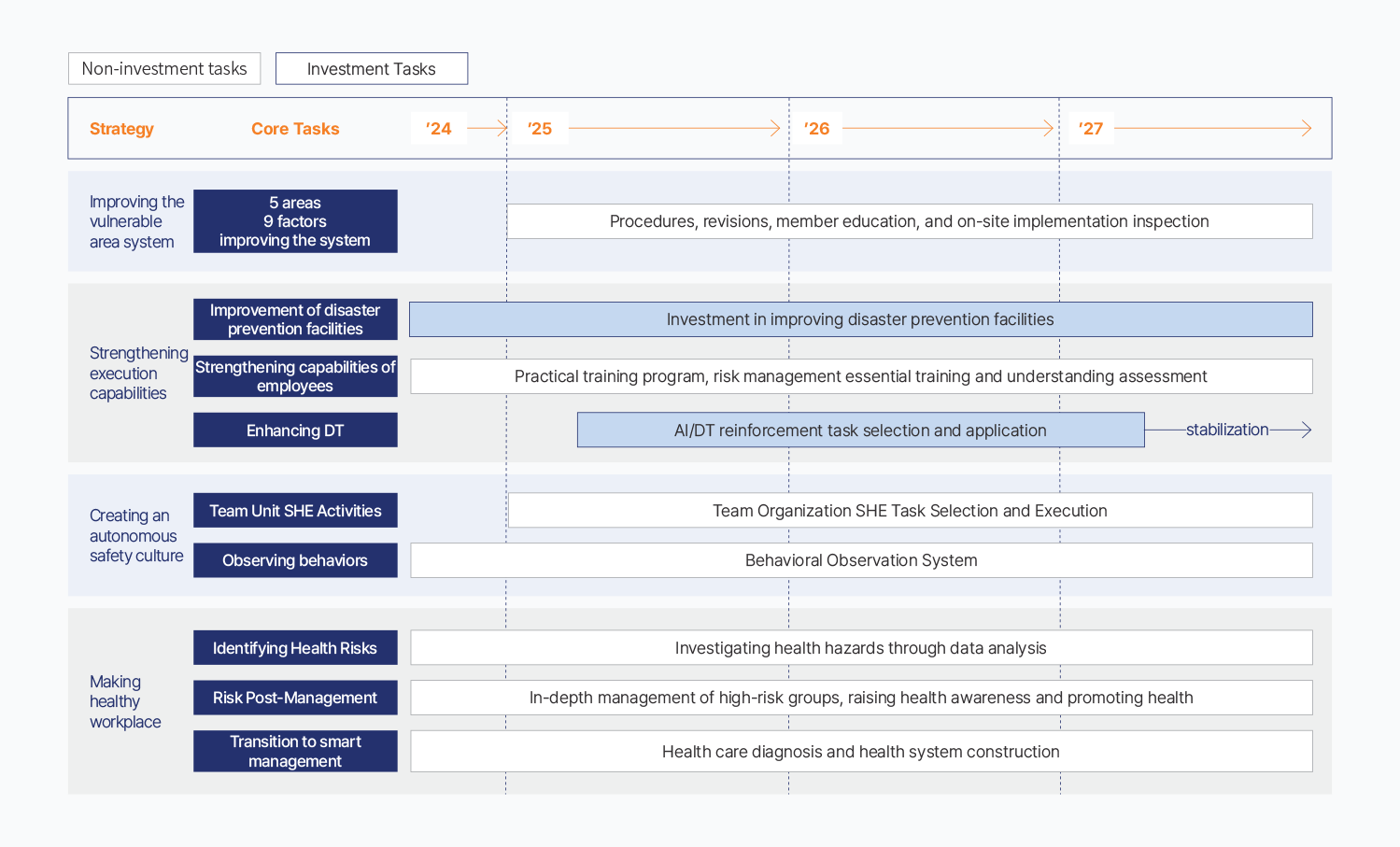
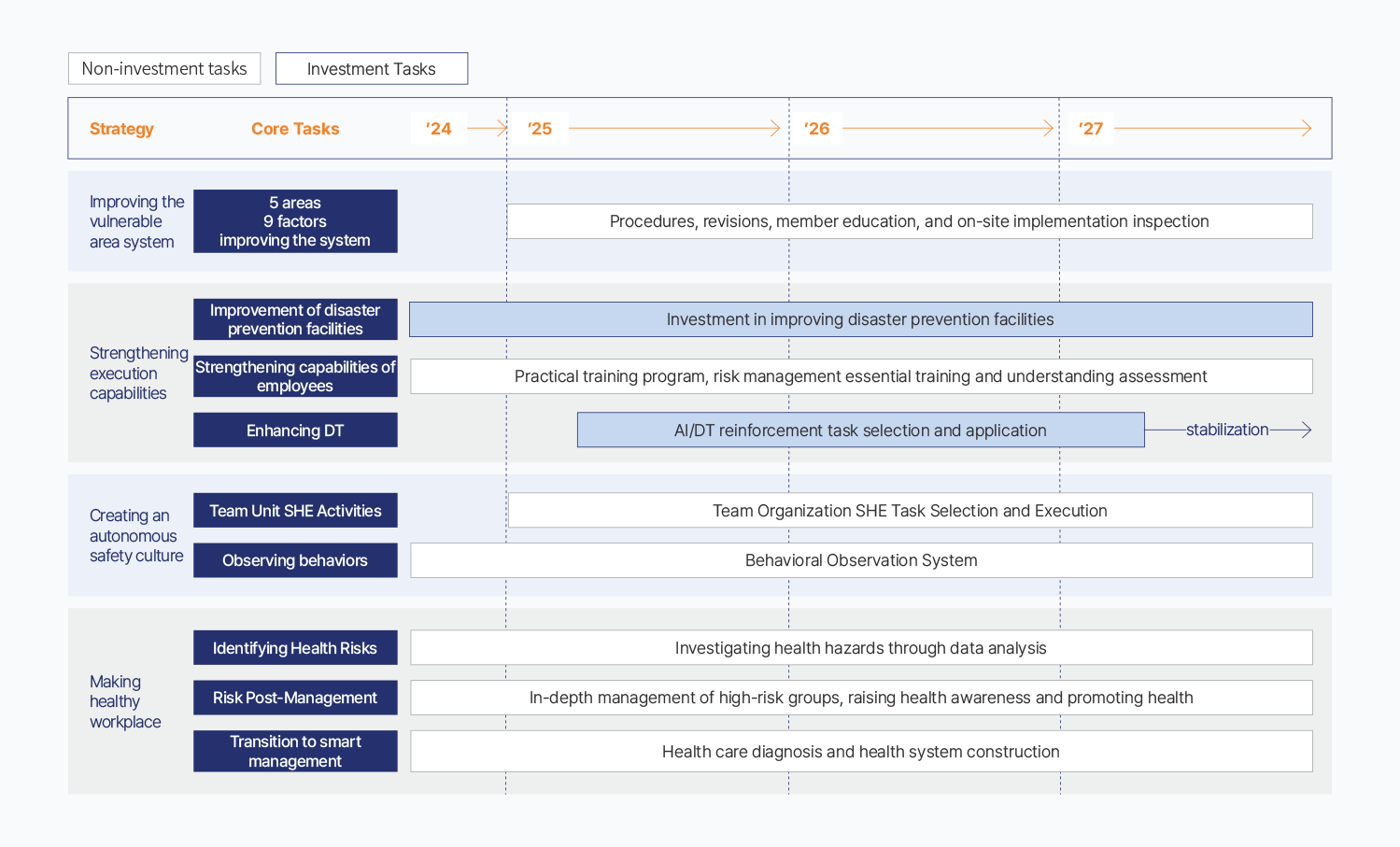
Governance
Organization
The CEO, as the Chief Safety Management Officer, is responsible for making decisions related to budgets, personnel, and other aspects of company-wide safety and health management, as well as overseeing the establishment and implementation of the SHE (Safety, Health, Environment) management system across all business sites.
To ensure effective company-wide industrial safety and health management, the SHE Promotion Team is established directly under the CEO, granting it independence and enhanced authority. This team formulates the overall SHE management strategy and monitors and supports the implementation of SHE strategies for each business site.
For each business site, a decision-making body called the SHE Committee and an execution body known as the SHE Team are established. The SHE Committee at each site consists of User Representatives, including site managers and department heads, as well as Worker Representatives, which include supervisors, department members, and members of the Happiness Council. The SHE Team at each site is composed of essential personnel across five areas: industrial safety, gas, fire prevention, chemical substances, and the environment, as required by relevant laws and regulations. Their responsibilities include conducting on-site inspections, promoting accident prevention programs, and carrying out related tasks.
Meanwhile, under the SHE Promotion Team, there is an organization dedicated to providing specialized safety management services to clients. This organization is responsible for inspecting the integrity of client facilities, supporting tenants in establishing safety management systems, and enhancing the capabilities of related partner companies.
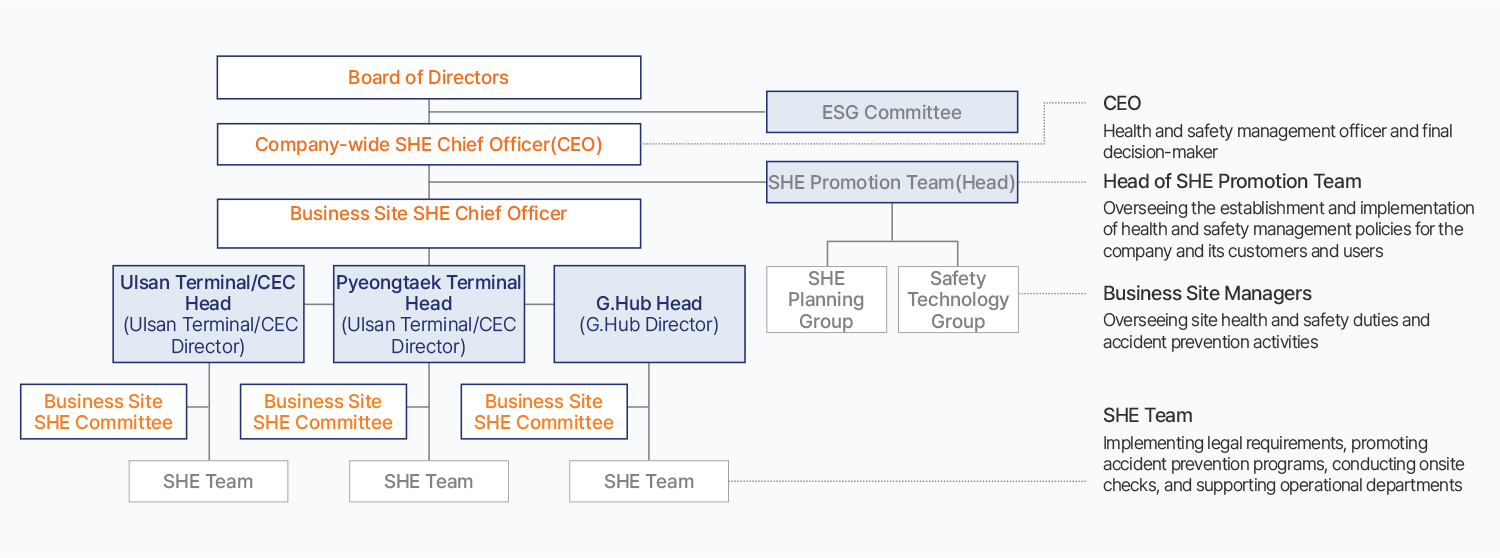
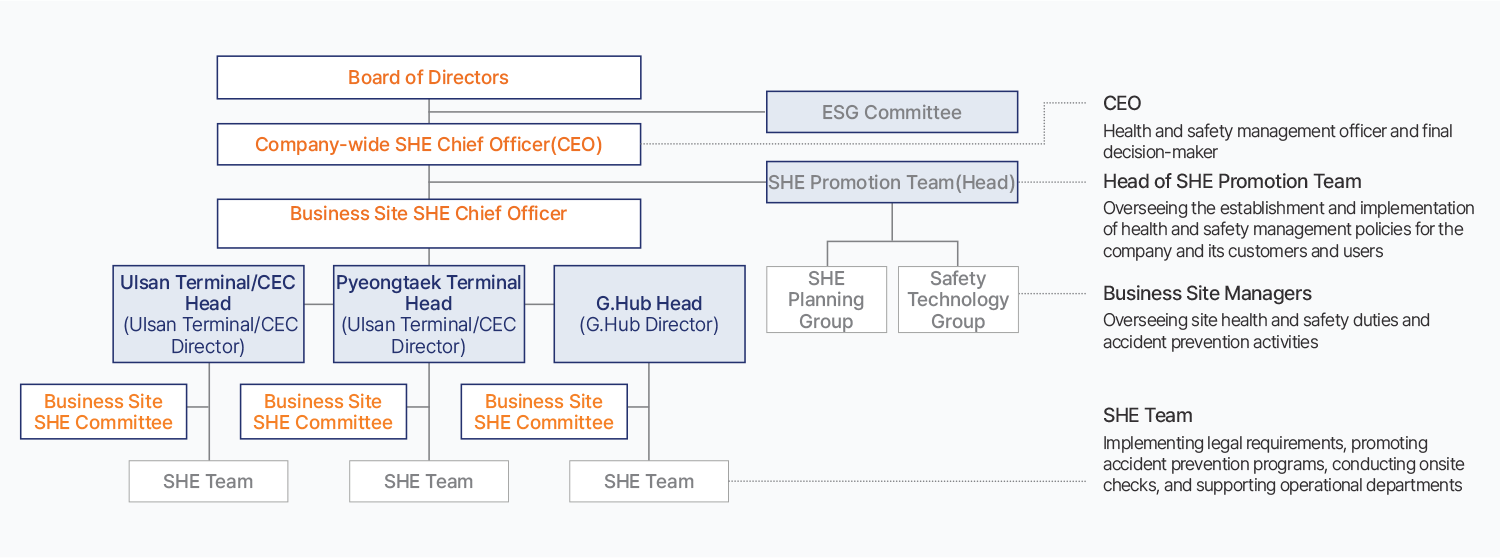
H&S in Workplaces
Risk management
Health and Safety Management Evaluation
To verify the level of health and safety management at its business sites from a professional and objective perspective, SK Gas conducts SHE (Safety/Health/Environment) management diagnoses through external expert organizations and group-affiliated experts. Based on the results of these diagnoses, SK Gas identifies directions for improving SHE management across its business sites, and inspects and improves the status of health and safety regulations compliance and facility management. These external diagnoses consist of reviewing regulations/procedures, conducting member interviews, and performing on-site verification. Improvement issues identified in the diagnosis results are classified according to their urgency as major non-conformities, minor non-conformities, and recommendations for improvement.

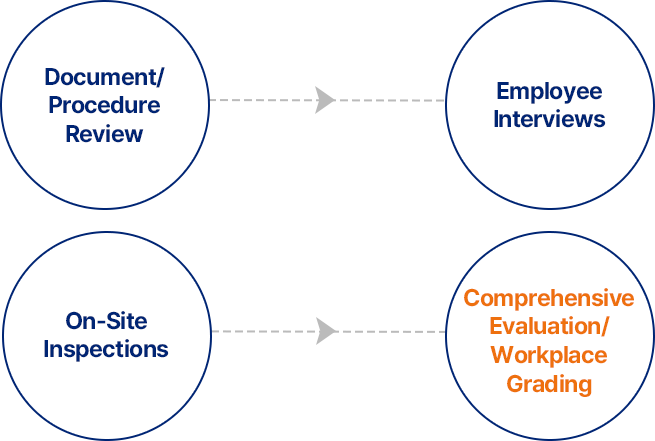
- Document/Procedure Review
- Employee Interviews
- On-Site Inspections
- Comprehensive Evaluation/Workplace Grading
Identification and Improvement of Safety Management Blind Spots
To identify potential health and safety risks, SK Gas lists all work activities within its business sites and conducts risk assessments to uncover any blind spots in safety management that may have been omitted from the management scope.
Establishing a Cycle for Hazardous and Risk Factor Management
SK Gas's on-site hazard management cycle consists of three stages: ① clearly defining management standards for hazardous work, ② identifying and improving on-site hazards, and ③ analyzing data through an IT system. The IT system enables real-time monitoring of inspection results and improvement status through a mobile app, and allows for data analysis to be reflected in policies. For key risk management items, monthly theme inspections are conducted and reflected in improvements. Additionally, near-miss incidents are identified and shared through a near-miss reporting contest held for all members of each business site, and improvements are implemented for all reported near-misses to eliminate potential hazards.
Establishment of Emergency Response System and Conducting Emergency Drills
SK Gas, in addition to its accident prevention efforts, analyzes incident-specific scenarios and has established corresponding emergency response procedures and organizations. Each business site regularly conducts emergency response drills utilizing these incident-specific scenarios to strengthen its emergency response capabilities and incorporates measures to prevent recurrence of any incidents that occur. To respond swiftly to emergencies, each business site operates a 24-hour continuous surveillance system and implements action procedures according to emergency response grades. Furthermore, SK Gas operates an emergency contact network for rapid reporting and dissemination of information regarding emergencies at each business site, and maintains contact information for public institutions, fire departments, and emergency services in the vicinity of its business sites to minimize damage to the surrounding areas. Moreover, SK Gas operates its own fire brigade and participates in practical training programs hosted by the National Fire Agency to enhance the real fire response capabilities of its firefighters.
Category | Frequency | Participating Entities |
---|---|---|
Fire Suppression Drill | Semi-annual | In-house |
Annually | Regional fire station, nearby companies | |
Fire Evacuation Drill | Semi-annual | In-house |
Emergency Call Drill | Monthly | In-house |
Chemical Disaster Prevention Drill | Annually | In-house |
Marine Pollution Prevention Drill | Semi-annual | Korea Maritime Environment Management Corporation |
Confined Space Rescue Drill | Semi-annual | In-house |
Company-wide Integrated Control System
SK Gas's company-wide integrated control system, established to proactively detect and prevent environmental, industrial health and safety risks and issues, is equipped with real-time on-site monitoring, integrated facility management, and risk situation management functions. By providing comprehensive information on health and safety and the environment through video, digital twin, and indicator screens, it supports rapid decision-making from a holistic perspective within the SHE control room.
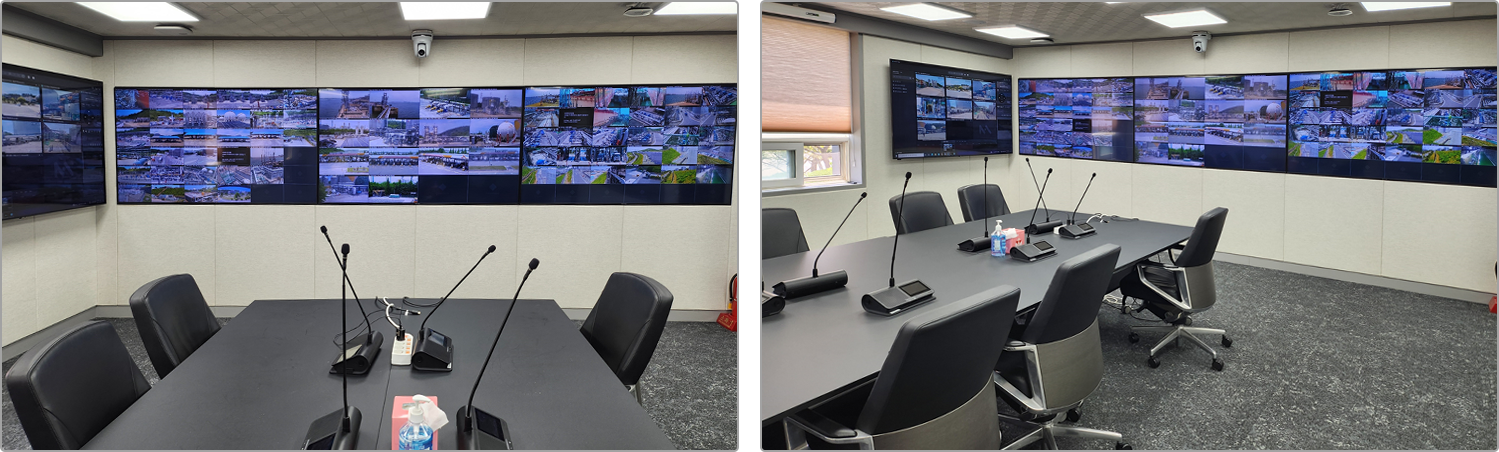
Ulsan Terminal Situation Room
Safety program
Building-up health and safety competence
SK Gas establishes educational plans and regularly operates programs to ensure that all employees, including those of contractors, fully recognize the importance of health and safety and are familiar with basic health and safety knowledge within the workplace.
① Regular Health and Safety Training
In accordance with safety-related laws and regulations such as the Occupational Safety and Health Act, all members receive mandatory regular health and safety training. Safety managers and other safety personnel, such as health and safety management supervisors, also periodically complete job-specific training.
Category | Skill / Training Course | Related Field |
---|---|---|
Statutory Training | Onboarding Training | Industrial Health and Safety Act |
Statutory Training | Training for Changes in Work Content | Industrial Health and Safety Act |
Statutory Training | Regular Supervisor Training | Industrial Health and Safety Act |
Statutory Training | Special Health and Safety Training | Industrial Health and Safety Act |
Statutory Training | Fire Safety Training/Drills | Act on Installation and Maintenance of Fire-Fighting Systems |
② Health and Safety Specialist Training
In addition to mandatory legal training, SK Gas enhances Safety competence through required and elective training programs tailored to the roles and seniority of business site members. Furthermore, SK Gas operates a Safety Specialist training course to develop personnel capable of conducting SHE diagnoses and providing support at business sites.
Category | Skill / Training Course | Related Field |
---|---|---|
SHE Capability Enhancement | HAZOP Leader Course | Process Hazard Analysis |
SHE Capability Enhancement | Process Safety Management (PSM) Report Writing and Implementation Status Assessment | PSM |
SHE Capability Enhancement | Enhancing Safety Management Competence of Contractors | Industrial Health and Safety |
SHE Capability Enhancement | Goal Management System and Emissions Trading Scheme Seminar | Greenhouse Gases |
SHE Capability Enhancement | Practical Safety Management of Hazardous Chemical Handling Facilities | Chemicals |
SHE Capability Enhancement | NEPA Code Interpretation | Hazardous Materials |
SHE Capability Enhancement | Workplace Accident Investigation and Countermeasure Establishment | Accident Investigation |
③ Hands-on Training Programs
To overcome the limitations of theory-based industrial health and safety education, SK Gas has developed and operates hands-on training programs aimed at strengthening members' emergency response capabilities and preventing serious accidents. Focusing on four vulnerable areas (equipment, high-altitude work, scaffolding, and electricity) and live fire response training, these programs encourage direct participation, allowing members to learn through experience, thereby enhancing accident prevention competence and on-site execution capabilities.
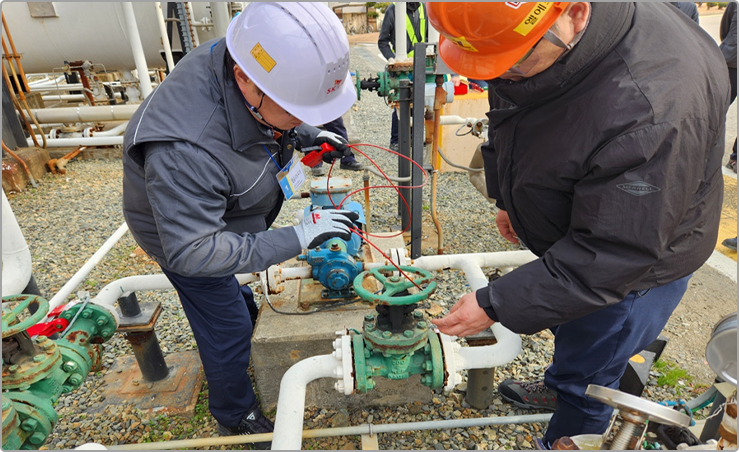
LOTO (Lock-Out, Tag-Out)
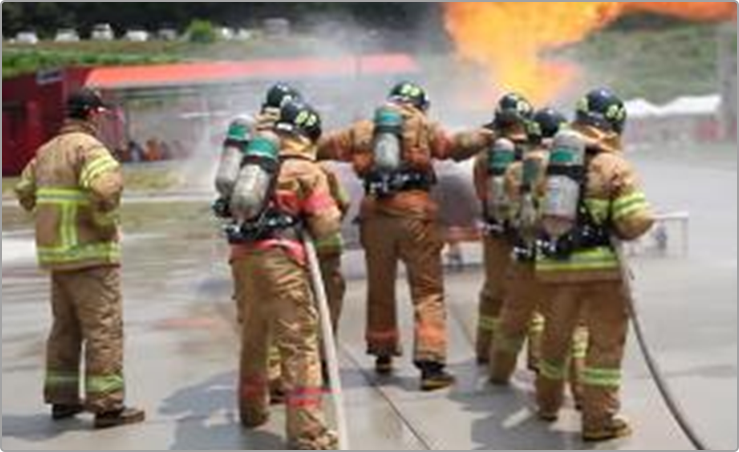
Live Fire Response
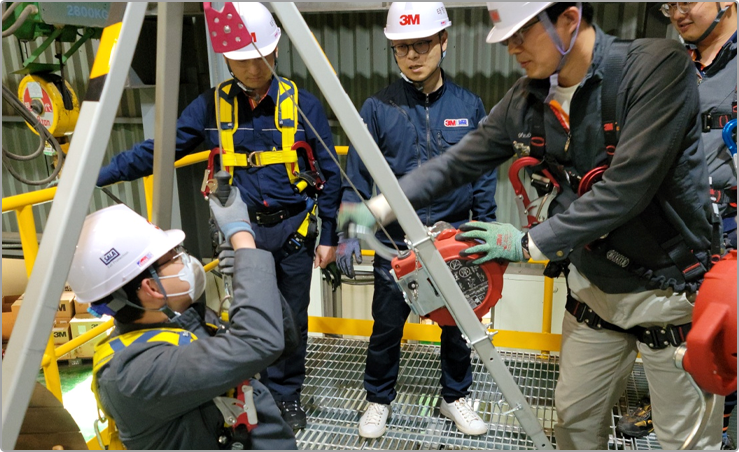
Working at Heights
SHE Rewards and Disciplinary System
SK Gas links its SHE reward/penalty system to provide various rewards, such as overseas training, to members who demonstrate excellent health and safety performance. Simultaneously, the company strives to establish a culture of adhering to SHE standards and procedures through disciplinary actions for violations of basic safety rules, legal requirements, and other demands of the health and safety management system.
Furthermore, SK Gas motivates its contractors to comply with health and safety management systems by awarding CEO commendations and prize money to companies with outstanding accident prevention activities or significant contributions to achieving zero accidents. By regularly selecting contractor workers who actively participate in accident prevention activities, such as identifying potential hazards, and providing them with health and safety activity incentives, SK Gas aims to emphasize the importance of joint participation in health and safety activities and encourage continuous involvement.
Collecting Employee Feedback
SK Gas specifies procedures for collecting the opinions of members and contractor workers in regulations such as the SHE Committee Operation Procedure and the Contractor SHE Management Procedure. Accordingly, each business site regularly holds Industrial Safety and Health Committees, Business Site SHE Committees, and Business Site SHE Communication Meetings, and actively reflects the collected opinions in policies and implementation to strive to create a safe working environment for all members.
Communication Channels
Category | Composition and Topics |
---|---|
Industrial Health and Safety Committee (Quarterly) |
|
SHE Committee (Quarterly) |
|
SHE Communication Meeting (Monthly) |
|
Health program
Employee Health
SK Gas supports occupational disease prevention activities and health promotion welfare systems for all members, including contract workers, to ensure a happy and healthy work life. To prevent occupational diseases, the company conducts workplace environment measurements and musculoskeletal risk factor surveys at each business site and operates an in-depth management system for high-risk members. In addition, SK Gas runs various welfare systems and programs for the health of its members, including psychological counseling programs, and improves these systems annually by listening to member feedback.
Employee Health Management Measures
Occupational Disease Prevention Activities | Health Promotion Welfare Programs |
---|---|
|
|
Focused Health Care Program
SK Gas aims to enhance health welfare for employees and partner company workers through the Focused Health Care Program for employees with health findings. By analyzing past check-up data, the program identifies individual health conditions and provides health habit formation messages, remote health consultations via AI chatbots, and offline programs with customized exercise and diet plans.
H&S for Contractors
H&S program for Contractors
Management Process
SK Gas ensures the suitability of partner companies through SHE evaluations and strengthens the quality and safety site management system to ensure that not only employees but also partner company workers can work in a safe environment. Safety management for work sites is based on the following three principles to review and confirm the implementation of various risk factors at different stages, aiming to prevent industrial accidents.
Three Principles of Safe Work
- 1Thorough risk assessment and safety measures before work
- 2On-site presence of safety officers
- 3Work stoppage in dangerous situations by anyone
Parner Health and Safety Support Programs
Health and Safety Support Systems for Partner Companies
SK Gas incorporates health and safety capabilities into the evaluation criteria for selecting contractors to ensure health and safety in contracted work. Accordingly, existing partner contractors are regularly reassessed for their health and safety capabilities based on these criteria, and new contractors must pass these evaluation criteria to participate.
For smaller contractors, SK Gas provides support through health and safety management consulting and training to establish management systems for risk assessment, work procedures, and training. High-risk contractors that fail to pass regular SHE evaluations are given opportunities to strengthen their capabilities through consulting and re-register through re-evaluation.
Furthermore, to improve on-site safety management levels and strengthen accident prevention, SK Gas has introduced a high-risk work management training certification system.
Win-win Cooperation Programs
Business Title | Program Name | Description |
---|---|---|
ECO-Hub | Potential Risk/Blind Spot Detection Program | Identification of blind spots to remove hazardous/risk factors and prevent accidents, selection and rewarding of best practices |
Ulsan Terminal | SHE Shared Growth Workshop | Group discussions for SHE shared growth, SHE quiz competition and awards, SHE commitment ceremony |
Pyeongtaek Terminal | Near-miss Incidents Detection Contest | Identification and evaluation of near-miss incidents to eliminate potential risks, with rewards for identified cases |
Internal Safety Broadcast Contest | Internal safety broadcast contest to establish and promote a voluntary safety culture | |
G.Hub | Partner Safety Keeper Activities | Identification and improvement of hazardous/risk factors, evaluation, and rewarding |
Emergency CPR Contest | Understanding emergency CPR procedures and enhancing emergency response capabilities, with evaluation and rewards |
Collecting Feedback from Partners
SK Gas's industrial health and safety policy includes contractors, special workers, service providers, and other partner companies. Accordingly, each business site manager listens to health and safety-related difficulties through contractor consultative bodies, meetings with contractor representatives, etc., and actively reflects the presented opinions. Furthermore, to receive grievances from contractor workers through various channels, SK Gas operates ethical management counseling/reporting channels and human rights counseling/reporting channels to receive and address their concerns.
Communication Channels for Partners
Site | Channel | Composition and Topics |
---|---|---|
ECO-Hub | Partner Council (Monthly) |
|
Ulsan Terminal Pyeongtaek Terminal G.Hub |
Partner Council (Monthly) |
|
Partner Representative Meeting (Monthly) |
|